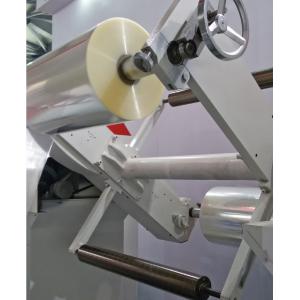
Add to Cart
Allfine Group-20 years experience Solution
1:Label production line- flexo print machine,die cutting machine,slitting machine,inspection and rewinding machine
2:Flexible package line-water bottle label PVC,heat transfer Pet, Opp, Pe etc rotogravure printer, dry laminator, PP PE film blowing machine,bag making machine
3:Decal paper,wine and smoking package-Silk screen press machinery, wicket dryer, uv dryer
4:Paper cup production line- flexo printer. die cutting machine, paper cup making machine
1: Save material 2: Improve efficiency 3:Professional tranning 4: Factory built
Partner Manager-Jack Huang
Allfine Group
ELS Automatic Plastic Film Printing Machine For Sale 300m/min 750mm unwind/rewind 3-50kgf servo motor
rotogravure printing production line.pdf
OPP | 18~60μm | PET | 12~60μm |
PE | 40~80μm | BOPP | 19~60μm |
CPP | 20~60μm | NY | 12~50μm |
PVC | 20~80μm | ||
Paper | 30~80g/ m2 |
Usage:
This machine is suitable for continuous ,multi-color printing or rolling material in good printing performance such as tobacco packing,yew paper,liquid paper box,BOPP,PET,NY,PVC and so on.
Feature:
1. Electronic line shaft for drive, servo motor drive for every color unit.
2. Free-standing master station, touch screen concentration control
3. Multi-sectional independent full automatic tension control, dancing roller inspection, tension display
4. Shaft-less printing cylinder with air chucking mechanism
5. Integral doctor blade mechanism
6. Pre-registration function, longitudinal and lateral automatic registration system.
7. Ink curtaining trolley
8. Uniquely designed high effective drying system
9. Optional heating source: electricity, steam, thermal oil or gas
Color quantity | 4 |
Max. Width of printing | 800mm |
Mechanical speed | 320m/min |
Printing speed | 300m/min (Variable because of different ink, film, familiarity of operator) |
Length of printing cylinder | 480~1000mm |
Dia. of printing cylinder | Φ120mm~Φ320mm |
Color control precision | ±0.10mm (Variable because of different ink, film, familiarity of operator) |
Max. unwind/rewind Dia.: | Φ750mm |
Tension range | 3~50kgf |
Tension control precision | ±0.5kgf |
Paper core diameter | 3 |
Core, I.D. of raw material | Φ76mm |
Pneumatic source | 0.6Mpa |
Impression roller pressure | 370kgf |
Doctor blade transverse move range | ±5mm |
Drying mode | Electrical heating |
Heating power(power of drying) | 50×6=300Kw |
Mail motor | 4Kw(6 SET) |
Power consumption | 380 KW |
Machine size | 22000×4400×3500(mm) |
Machine weight | Near 30000kg |
Automatic speed up/down to the target speed gradually | |
Max. speed limit can be set for different material or cylinder size | |
Idle or running status can be exchanged |
Sequ. | Item | Specification | Unit | Quantity | Notes |
1 | Leveling pad | Set | 1 | Attachment | |
2 | Wrench | 8X10 | pc | 1 | Tool |
3 | Wrench | 14X17 | pc | 1 | Tool |
4 | Wrench | 19x22 | pc | 1 | Tool |
5 | Adjustable wrench | 200mm | pc | 1 | Tool |
6 | In Hex wrench | 4,5,6,8,10mm | pc | 1 for each | Tool |
7 | Screw driver | 150 | pc | 1 | Tool |
8 | + screw driver | 150 | pc | 1 | Tool |
9 | Oil gun | pc | 1 | Tool | |
10 | Grease gun | pc | 1 | Tool | |
11 | Thermometer | pc | 1 | Spare | |
12 | Solid relay | pc | 1 | Spare | |
13 | AC Contactor | pc | 2 | Spare | |
14 | AC Contactor | pc | 2 | Spare | |
15 | Start button | pc | 2 | Spare | |
16 | Stop button | pc | 2 | Spare | |
17 | Indicate lamp | pc | 2 | Spare | |
18 | Heating tube | pc | 2 | Spare | |
19 | Rubber roller | L=00mm | pc | 6 | Attachments |
20 | Rubber roller | L=00mm | pc | 6 | Attachments |
22 | Ink pump | pc | 6 | Attachments | |
23 | Cylinder shaft | pc | 6 | Attachments |
1)Electrical parts
Name | Manufacturer | Model | Remark |
Inverter | Japan Yaskawa | ||
Main low-voltage appatatus | France Schneider | ||
Indicator light, button | France Schneider | ||
PLC | Germany Siemens | ||
2)Mechanical part
Name | Manufacturer | Model | Remark |
Guide roller | Self-made | Φ80 | treatment of static and dynamic balance |
Top roller | Self-made | ||
motor | Siemens | ||
Rewinder | 3kw AC vector converter | Y132M-4 | |
unwinder | 3kw AC vector converter | Y112M-4 | |
traction | 1.5kw AC vector converter | Y112M-4 | |
synchronization belt | Shanghai | ||
Main bearing | NSK |
3)Pneumatic part
Name | Manufacturer | Model | Remark |
Pneumatic components | Taiwan Airtac | ||
Joints, three-joint assembly | Ningbo | ||
Electromagnetic valve | Taiwan |
Note:
For user prepare for:
Statement:
1. The ink types, materials, printing area will effect printing speed.
2. Since this model is one of the high-tech products, according to the design requirements, we reserve the right to change some structure and parameters in order to provide you better equipment.
Video:info me for the mp4
Platemaking[3]
The first method of plate development uses light-sensitive polymer. A film negative is placed over the plate, which is exposed to ultra-violet light. The polymer hardens where light passes through the film. The remaining polymer has the consistency of chewed gum. It is washed away in a tank of either water or solvent. Brushes scrub the plate to facilitate the "washout" process. The process can differ depending on whether solid sheets of photopolymer or liquid photopolymer are used, but the principle is still the same. The plate to be washed out is fixed in the orbital washout unit on a sticky base plate. The plate is washed out in a mixture of water and 1% dishwasher soap, at a temperature of approximately 40 °C. The unit is equipped with a dual membrane filter. With this the environmental burdening is kept to an absolute minimum. The membrane unit separates photopolymer from the washout water. After addition of absorb gelatine for example, the photopolymer residue can be disposed of as standard solid waste together with household refuse. The recycled water is re-used without adding any detergent.[4]