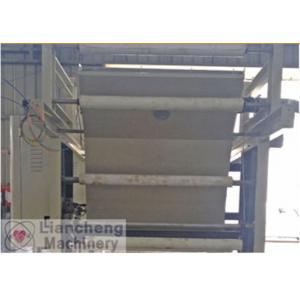
Add to Cart
Allfine Group-20 years experience Solution
1:Label production line- flexo print machine,die cutting machine,slitting machine,inspection and rewinding machine
2:Flexible package line-water bottle label PVC,heat transfer Pet, Opp, Pe etc rotogravure printer, dry laminator, PP PE film blowing machine,bag making machine
3:Decal paper,wine and smoking package-Silk screen press machinery, wicket dryer, uv dryer
4:Paper cup production line- flexo printer. die cutting machine, paper cup making machine
1: Save material 2: Improve efficiency 3:Professional tranning 4: Factory built
Partner Manager-Jack Huang
Allfine Group
LC-B Model Series of water based gravure ink color printer Cellophane NY PVC PET BOPP CPP PE OPP Paper film alu 70m/min
rotogravure printing production line.pdf
Main components"
1.Unwinding and traction units........................................1 unit
2.Printing units.................................................................6 unit
3.Rewinding and traction units........................................1 unit
4.Computer color register................................................1 set (optional) Shangxi Kesai 2000CX for the Vertical
Printing Material | |||
OPP | 18~60μm | PET | 12~60μm |
PE | 40~80μm | BOPP | 19~60μm |
CPP | 20~60μm | NY | 12~50μm |
PVC | 20~80μm | ||
Paper | 30~80g/ m2 |
Note:
1) three-phase and four-line
2) switch by air
3) 380V 50Hz
Usage:
This machine is used for BOPP,PET,PVC,PE Rolling Paper etc with good printing performance of rolling material for multi-color continuous printing.
Feature:
1. 360-Degree printing plate aligning device, easy operation.
2. Obturated oven, automatic constant temperature system.
3. Magnetic powder brake control for unreeling and traction reeling with moment motor.
4. Reeling in and unreeling at dual stations, semi-automatic material change without machine halt.
5. One-off printing on both sides.
Technical Parameters | |
Printing color number | 6colors (possible to add or reduce printing color class) |
General printing base material | Cellophane: 20-30um |
Max width of base material | 620mm (we also have 820, 1020, 1220, 1420, 1620, 2520mm) |
Max speed | 90m/min |
Printing speed | 10-70m/min |
Vertical comprehensive colored precision | ±0.1mm |
Diameter of printing roller | 90mm-380mm |
Max width of printing roller | 650mm |
Width of guide roller | 650mm |
Diameter of guide roll | 600mm |
Machine color | offwhite (you can choose any other colors) |
Random accessories:
No. | Title | Spec & Code | Unit | Amount |
Tad for machine | Piece | 30 | ||
1 | Double head wrench | 8×10 | Piece | 1 |
2 | Double head wrench | 12×14 | Piece | 1 |
3 | Double head wrench | 14×17 | Piece | 1 |
4 | Double head wrench | 19×22 | Piece | 1 |
5 | Double head wrench | 27×30 | Piece | 2 |
6 | Inner hexagonal wrench | Sets | 1 | |
7 | - shape screw driver | Piece | 1 | |
8 | +shape screw driver | Piece | 1 | |
9 | Rubber pressure roller | 600,400mm (according to customer material max width) | Sets | 1 |
10 | Ink plate | 600,400mm(according to customer material max width) | Sets | 1 |
11 | Ink pump | Pieces | 6 | |
12 | Scraper (soft) | Piece |
Statement:
1. The ink types, materials, printing area will effect printing speed.
2. Since this model is one of the high-tech products, according to the design requirements, we reserve the right to change some structure and parameters in order to provide you better equipment.
3. Printing
A flexographic print is made by creating a positive mirrored master of the required image as a 3D relief in a rubber or polymer material. Flexographic plates can be created with analog and digital platemaking processes. The image areas are raised above the non image areas on the rubber or polymer plate. The ink is transferred from the ink roll which is partially immersed in the ink tank. Then it transfers to the anilox or ceramic roll (or meter roll) whose texture holds a specific amount of ink since it is covered with thousands of small wells or cups that enable it to meter ink to the printing plate in a uniform thickness evenly and quickly (the number of cells per linear inch can vary according to the type of print job and the quality required).[5] To avoid getting a final product with a smudgy or lumpy look, it must be ensured that the amount of ink on the printing plate is not excessive. This is achieved by using a scraper, called a doctor blade. The doctor blade removes excess ink from the anilox roller before inking the printing plate. The substrate is finally sandwiched between the plate and the impression cylinder to transfer the image.[6] The sheet is then fed through a dryer, which allows the inks to dry before the surface is touched again. If a UV-curing ink is used, the sheet does not have to be dried, but the ink is cured by UV rays instead.